Rustproof Steel
Stainless steel is a steel alloy of iron and carbon, to which chromium and sometimes nickel have been added. These elements prevent oxidation. Stainless steel contains at least 10,5 % of the total weight of chromium and at most 1,2 % of carbon.
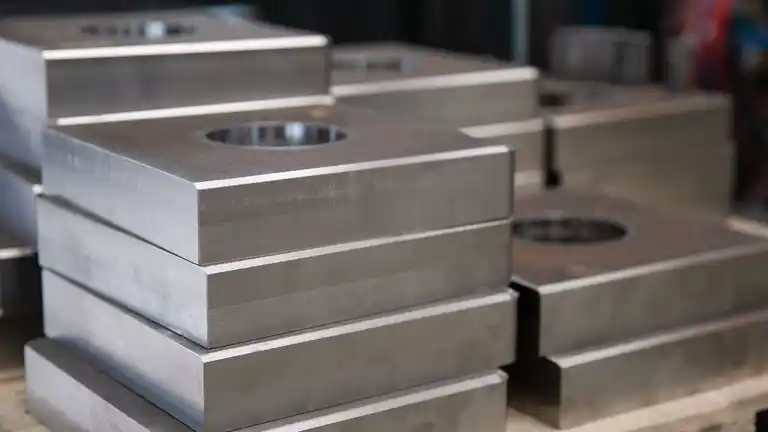
Material that contains chromium but no nickel can resist corrosion well, but is not called stainless steel but chromium steel.
Rustproof steel is also known as "Stainless Steel", "Inox", "18/8" or "NiRosTa". Contrary to popular belief, stainless steel can oxidize. In fact, the chromium in the surface of stainless steel oxidizes to chromium(III) oxide in combination with oxygen. This layer is only a few nanometers thick and protects the underlying steel from further corrosion.
Especially in aggressive environments with chlorine, salts or at high temperatures, however, certain types of rustproofed steel are insufficiently protected against corrosion and are therefore unsuitable. It is up to the engineer to choose the right type of steel to suit the application and the environment in which the rustproof steel will be used.
Based on the crystal structure, rustproof steel is divided into austenitic, ferritic and martensitic steels and also duplex.
Austenitic microstructure
This steel contains a relatively high proportion of chromium and nickel (6 to 26%). These two elements together make up at least 25% of the total alloy. 2 / 3 of all rustproof steel grades have an austenitic structure. The best-known grades are rustproof steel 304 and 316.
Rustproof steel 304 is also known as 18/10, where the proportions of chromium (18%) and nickel (10%) are specified. Rustproof steel 304 is also referred to as "V2A", stainless steel 316 as "V4A".
Rustproof steel 316 contains an additional 2% molybdenum, which gives it greater resistance to corrosion.
Ferritic microstructure
Rustproof steel with a ferritic structure consists mainly of iron and carbon. Chromium is mainly added as an alloying element, which can have a content of 13 to 18 %.
It is possible that other alloying elements such as niobium, titanium or zirconium can be added to give the material even better properties. These elements can for example improve weldability and increase hardness.
These steel grades are slightly magnetic and cannot be hardened due to heat treatment.
Martensitic microstructure
The main characteristic of martensitic stainless steel is that it is hard wearing. Its composition is similar to ferritic rustproof steel and it is also magnetic.
In the unhardened state, this steel has a ferritic structure and only forms a martensitic crystal structure after hardening and tempering. In this form it is less corrosion resistant than ferritic rustproof steel.
On the other hand, the material is harder and has a high yield strength. A higher carbon content results in a higher achievable hardness and tensile strength. By tempering the product, the tensile strength will decrease slightly, but the ductility will increase again.
Duplex Steel
Duplex steel consists of a combination of ferritic and austenitic crystal structures within the same material. The material offers some of the advantages of both crystal structures.
The yield strength can be twice as high as that of austenitic stainless steel. Other advantages include a lower coefficient of expansion, increased hardness and improved weldability and ductility.
In terms of corrosion resistance, Duplex is more resistant to stress corrosion. Due to its hardness, however, it is less easily deformable. The temperature range in which duplex variants can be used is normally limited to +280°C.
The applications of stainless steel
Because stainless steel is more expensive than structural steel, the right choice must be made where rustproof steel is needed and which variant should be used. Rustproof steel is generally resistant to corrosion, but the different variants each have their own area of application. The most commonly used types of rustproof steel are steel 304 and steel 316.
Steel 304 is less resistant to salts and chlorides. Steel 316 is more resistant to these chemicals and is therefore better suited for use in aggressive environments. However, steel 316 may not be suitable for use where chlorides are a problem. For example, a staircase leading out of a swimming pool can be made of that steel grade, but it is unwise to make heavy-duty components of steel 316. It is better to use a duplex variant for this.
Determination of corrosion resistance (PREN)
The corrosion resistance is indicated by the PREN value. PREN stands for "Pitting Resistance Equivalent Number" and can be calculated using the following formula:
PREN = 1 x %Cr + 3,3 x %Mo + 16 x %N
PREN | Resistance class | Applications |
---|---|---|
17,0 - 21,3 | II / moderate | no higher exposure to chlorides and sulphur dioxides |
23,1 - 28,5 | III / medium | moderate exposure to chlorides and sulphur dioxides |
41,2 - 48,1 | IV / strong | high exposure to chlorides, sulphur dioxides and water steam |
Mechanical properties
Austenitic rustproof steel can be hardened by cold forming (e.g. bending). The specific mass of rustproof steel (7,930 kg/m³) is slightly higher than that of steel (7,800 kg/m³). For both materials, a worldwide trade charge of 8,000 kg/m³ is calculated.
To calculate the structural deflection, the modulus of elasticity is important. For stainless steel this is between 193 and 204 kN/mm² (GPa) and therefore does not differ significantly from steel (210 kN/mm² (GPa)). However, the coefficient of expansion of austenitic rustproof steel (approx. 16 µm/m °K-1) is significantly higher than that of structural steel (approx. 10 µm/m °K-1). A structural engineer will have to take this into account, especially if longer lengths or high operating temperatures are to be expected.
Duplex steel offers a solution to this problem. The coefficient of expansion of the duplex variants is approximately 10 to 11 µm/m °K-1, which is practically the same as that of mild steel. The typical tensile strength of rustproof steel is between 480 and 700 N/mm². The yield strength (Rp 0.2) is approximately between 180 and 300 N/mm². However, many variants of rustproof steel have been developed, so these values only serve as a general guideline.
Trivia
In 1912, the Brown Firth Research Laboratories under the direction of Harvey Brearly (1871 - 1948) were charged with investigating the wear in the barrels of firearms and cannons. This wear was mainly due to the high temperatures generated when firing the guns. Harvey came up with the idea of adding chromium (Cr) to the steel alloys to increase the melting point of the steel.
But when the alloy was exposed to acid, nitric acid thinned with alcohol, the material proved to be unexpectedly acid resistant. Harvey has since been considered the (accidental) inventor of rustproof steel. The first rustproof steel was cast on 13 August 1913. Originally it was announced as a material that would be very suitable as cutlery for e.g. cruise ships and hotels.
See also
BRINAR
BRINAR is a wear-resistant steel which is used in mechanically highly stressed areas.
Read moreConstruction Steel
Construction steel has excellent mechanical properties and can be processed very well.
Read moreCopper
Copper is used in many ways for industrial and construction purposes. It is also suitable as an alloying element.
Read more