Microstructure
Under high magnification you can see that steel has a granular structure. This structure is formed during the cooling process of molten steel when freely moving atoms combine to form crystals. Different temperatures, cooling rates and carbon saturation result in different microstructures.
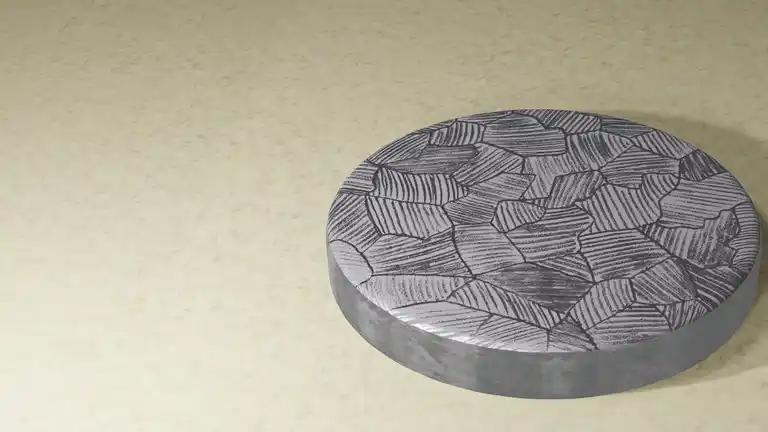
If we look at the iron-carbon diagram (EKD), the example of a eutectoid steel with 0.8 % C illustrates how the structure is formed.
An imaginary vertical line in the EKD through the so-called eutectoid point at 723°C, passes through different areas of the EKD with the different lattice shapes during slow cooling. At 0.8 % C, no precipitation of carbon takes place during cooling, since the austenite has sufficient interstitial lattice spaces up to 723°C.
At 723 °C this lattice flips over into a body-centered cubic lattice with much lower solubility than the face-centered cubic lattice. The now excess carbon combines with iron to form Fe3C, the cementite or iron carbite, with the neighbouring part of carbon depleting and forming the ferrite, the Alpha Mixed Crystal.
This very rapid interaction produces the lamellae of ferrite and cementite, which are visible in the structure and are called perlite. The more carbon is present in the steel, the more perlite is formed in the microstructure and has a dramatic effect on the mechanical-technological properties.
Hypo-eutectoid steels (C content < 0.8 %) have a ferritic-pearlitic microstructure Fig. 1) and hyper-eutectoid steels have a microstructure of perlite and cementite Fig. 3, which is formed at the grain boundaries due to the decreasing solubility of austenite for carbon.
As a rule of thumb: Up to 0.2% carbon, the steel is easily weldable and cold and warm formable, above 0.2% carbon these properties decrease and strength and hardenability increase.
See also
Brinell hardness test
Performing the hardness test by means of a ball pressure test according to the Swedish engineer Johann August Brinell.
Read moreCoil
Plate metal that is rolled-up to coils is easier to transport and requires less space in the warehouse
Read moreCorrosion
Corrosion is a natural process and damages most metals. What types of corrosion are there?
Read more