Weld Preparation
Before workpieces can be welded together, the welding edges must be prepared. On one hand this is necessary to achieve optimum dimensional accuracy and on the other hand it is important to prevent undesirable substances from entering the weld pool, which could have a negative influence on the quality of the weld seams.
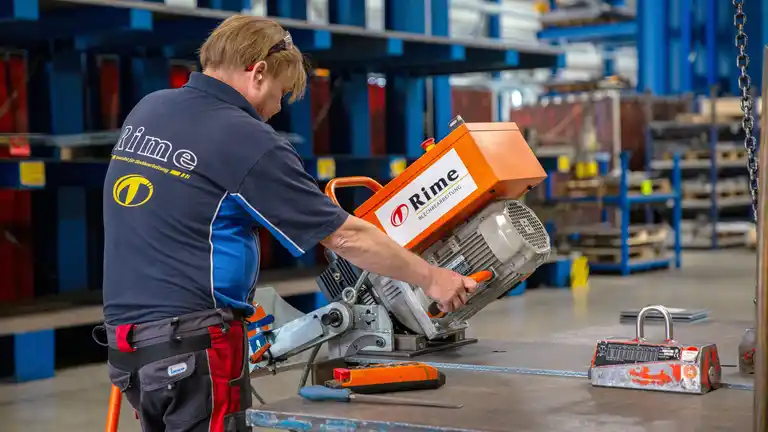
Cleaning the welding joints
Before workpieces are welded together, weld joints must be cleaned of oil, grease, wax layers and paint. The welding joints must be metallically clean so that the workpieces can be joined together in an optimum manner.
When cleaning mechanically, it is essential to ensure that no coolants or lubricants are used.
If the weld seam preparation is carried out on aluminium, it must be ensured that abrasives have been expressly recommended for aluminium by the relevant producer. Sandblasting is also possible for preparing the weld seam. Here too, the abrasive must match the material.
Manual cleaning is also possible for preparing the welding seam. Only stainless steel brushes should be used for this. With other brushes it is possible that inclusions of carbon steel may occur in the base material. The diameter of the bristols should be between 0.1 and 0.25 mm. Bristles that are too thin only smear the dirt and wires that are too thick cause deep scratches on the surface to be welded.
In general, turning, milling or other chip removing processes are very suitable for cleaning the welding points.
Nibbling chamfers
Nibbling is a fast and inexpensive method for the preparation of welding seams. With our edge milling machine we can produce chamfers in the angle range from 20° to 45°. The maximum sheet thickness is 15 mm. That machine works with a sharp cutting wheel of hardened steel.
On the one hand, this cutting wheel acts with very great force on the edge of the material, which creates the desired chamfer for the welding process. By rotating the wheel, the entire machine is simultaneously moved along the edge of the plate metal until the bevel is applied to the full length.
The chamfer resulting from the nibbling is very precise in terms of angular accuracy, but has a rough surface, which is caused by the pressure of the cutting wheel. However, this ripple pattern is not relevant for the later welding process, because the material is completely melted during welding.
Milling and laser cutting are also two good methods of adding chamfers to workpieces. With these methods we can produce chamfers in various sizes and angles on request. Compared to nibbling, these processes are more cost-intensive and are only rarely worthwhile as weld seam preparation.