Spot Welding
Spot welding is a resistance welding procedure and is a method that does not require shielding gas.
The workpieces to be joined are placed on top of each other precisely in the first step. Two electrodes press the two workpieces together mechanically and fix the parts to be welded.
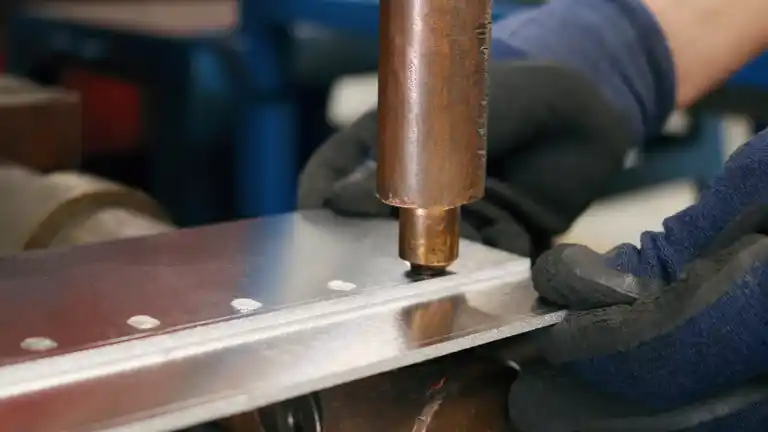
By supplying an electrical power, a current flows between the two electrodes. The workpieces represent a resistance for the flowing current. This causes the metal to heat locally sufficiently to liquefy. The mechanical pressure of the electrodes causes the two workpieces to fuse together and after cooling they are inseparably joined.
1. Aligning the workpieces
In order to join the workpieces by means of spot welding they must be precisely aligned with each other, as correction after welding is not easy.
2. Pressing on the electrodes
Suitable electrodes are chosen for welding the workpieces. These are mostly made of copper alloys with fractions of tungsten and molybdenum, which can withstand the high temperatures and pressures.
3. The current is flowing
If the electrodes have been positioned correctly, the current is switched on, which flows from one electrode to the other with a very high power. The material is heated so much that it liquefies and so both workpieces join.
4. The workpiece are tightly joined
The time during which the electrical current must flow through the workpieces varies, depending on the material and workpiece thickness. If the parts are tightly joined, the electrodes are removed in order to repeat the process at the next welding point.
This welding procedure can be repeated as often as necessary, depending on the workpiece size. Therefore, despite the small spot welds, a high degree of stability can be achieved.
Technical functionality
Spot welding is mainly done with alternating current. Direct current is also possible, but is rarely used.
For spot welding, so-called spot welding pliers are used. These are mainly used on mobile resistance welding equipment. Manual spot welding is used today in car repair shops or in handicraft businesses. In addition, spot welding can also be carried out by robots, which are known from the production of automobiles, for example.
Quality Control
If you want to check the quality of the spot weld, you have to pay attention to two things:
- The spot weld has the same colour inside as the plate metal
- The outer ring is brown, maximum blue
If these characteristics apply, the material has not been overheated and it can be assumed that no cracks have formed. In addition, the imprint should not be deeper than 20% of the sheet thickness.