Plate laser cutting of large and small parts
We use laser cutting as a separation process for plate metal made of steel, rustproof steel and aluminium. The cutting is CNC-controlled with modern cutting methods such as CoolLine and BrightLine.
Thicker plates can be cut up to a thickness of up to 30 mm with our fiber laser!
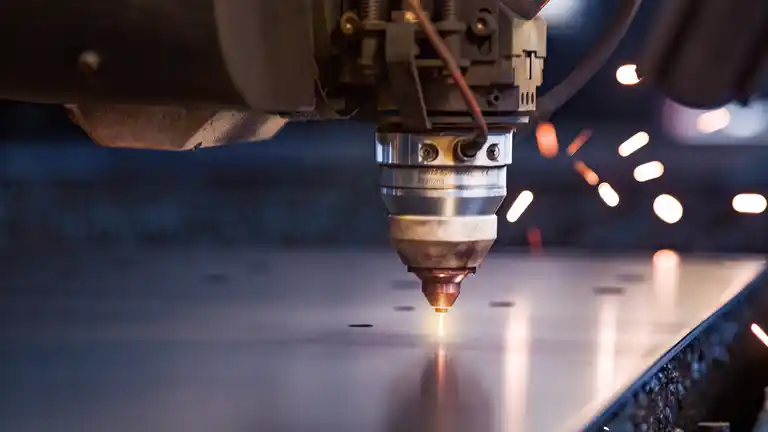
CNC laser cutting at Rime
Laser cutting is one of the most important processes in our company. For over 30 years we have been offering our customers laser cutting in the range of 6,000 to 2,000 mm. Over the years, we have continuously invested in the latest CNC machine technology to ensure that we can always offer our customers the best options in plate metalworking. Our laser department has also been significantly expanded over the last three years.
- XXL laser cutting of plates in the working area 16,000 x 4,000 mm
- In addition, three laser cutting machines for sheets in the 6,000 x 2,000 mm range
- Cutting of bevels up to 45 degrees and 16 m length
- Filigree plate cuts with the BrightLine cutting process from Trumpf
- High-quality plates with thicker materials with the Trumpf CoolLine process
Laser parts with higher material thicknesses
With our fiber laser, we can cut much higher material thicknesses. This machine has over 15,000 watts, which is almost three times the power of conventional laser systems. Due to the enormous output, this machine is not only able to cut thicker sheets, but also achieves a much higher cutting speed with thinner thicknesses.
Up to 150 meters per minute is the highest speed possible with this machine. The working area of this machine is 6,000 x 2,000 mm.
You have a question about our production capabilities?
We are happy to help you! Call us or simply write an E-Mail.
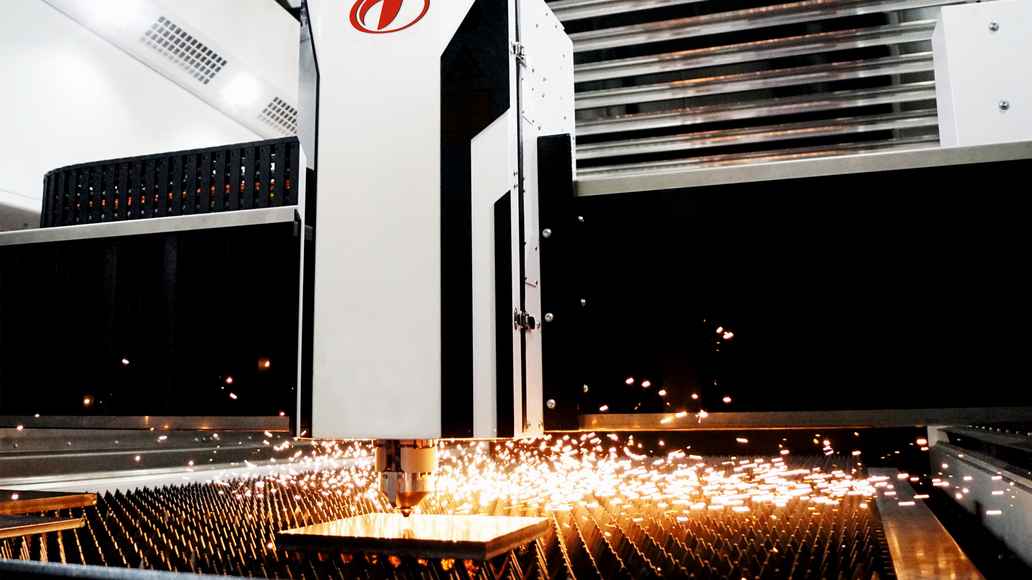
With our laser machines we are able to produce large and small parts effectively and in good quality.
Laser processing of large parts
In addition to the enormous working area of 16,000 x 4,000 mm, the machine offers the following advantages:
- Feeding and cutting take place simultaneously, which shortens job processing times.
- The machine is very robust and much easier to maintain. This reduces downtimes to a minimum.
- It has a bevel head that can cut bevels up to 45 degrees. Chamfering and material cutting are thus done in one operation.
- With this machine, we have increased our capacity many times over.
Laser cutting of bevels is possible up to 45° and 16 m length!
You would like to receive an offer? - No problem!
Send us a short E-Mail with your wishes.
Influence of the material quality on laser cutting
The quality of the cut surface depends very much on the material grade and its surface. Chemical structure and homogeneity of the material are important factors. Surfaces hardened by shot blasting, rust and scale can lead to a degradation of the laser cut quality. Scoring marks and wash-outs can form. For laser parts with high demands on the cut surface, there is material available which has been specially developed for laser cutting.
Advantages of laser cutting
- Cutting of steel, rustproof steel and aluminium with the same machine
- Production of almost every imaginable shape
- Simultaneous processing of several orders
- The use of inert gases eliminates the need for costly reworking
Are there also disadvantages?
Despite many advantages, laser cutting unfortunately also has a few economic and financial disadvantages.
- CNC laser cutting consumes a lot of energy.
- The use of shielding gases cannot be dispensed with.
Fusion cutting uses nitrogen, which is blown into the kerf at high pressure during the cutting process. Gas consumption is extremely high in large machines and represents a decisive cost factor.
Good to know
Another challenge is the thickness of the material. Our laser cutting systems can cut steel up to a thickness of 30 mm. The thicker the plate, the slower the cut must be made to cut through the metal completely.
The slower the laser beam cuts through the material, the more heat is introduced into the plate. The additional heat causes more material to be melted in the cutting gap than is actually desired.
This creates a characteristic pattern of ripples for laser cutting, which can be so strong that the edges of the material have to be reworked in order to ensure optimum product quality.
Another problem can occur with thicker workpieces. The laser beam is minimally deflected during piercing and thus creates a slightly slanted cutting edge.
This can affect the dimensional accuracy of the product. With low material thicknesses, the deflection of the laser beam does not play a significant role.
How is a laser cutting machine constructed?
With our laser cutting machines we can cut sheet metal plates of different formats. The heart of the system is the laser cutting head, which is moved in three axes via guide rails. By adjusting the Z-axis, the cutting head adapts to the height of the workpiece. Controlled feeds of the X and Y axes move the laser cutting head to any desired point.
The exact position, the sheet metal panel on the processing table, is determined by a three-point measuring procedure at program start. This allows a slight tilt of the material during cutting to be corrected. The cutting head is shielded with a protective cabin. This protects against dust and gas emissions as well as reflection of the laser beam.
The strong heating of the sheet metal during the cutting process leads to the vaporisation of elements such as chromium, nickel, copper or titanium from the plate metal, which in gaseous state have a hazardous effect on health. The extraction device with professional filter system in the protection cabin minimizes these emissions.
Laser Lens
The heart of a laser cutting machine is the cutting head in which the laser lens is placed. This is needed to bundle the laser beam. Only in this way does the beam achieve the necessary power to melt metals. After bundling, the beam is about 2,500 times stronger than before. The laser lens for a cutting system is not made of glass as in the case of magnifying glasses or binoculars, for example.
The laser lenses therefore consist of zinc selenide (ZnSe). This material is heat-resistant up to a temperature of 1,500°C and gives the laser lenses their typical orange colour.
In addition, the lenses are coated with a thin layer of thorium fluoride. Despite the colouring, laser lenses are absolutely transparent for light in the infrared range. Our Co2 lasers work in this spectral range, which is invisible to the human eye.
Laser cutting machine lenses come in a variety of shapes and sizes. The most common types of lenses are spherical, cylindrical, and aspheric. Spherical lenses are used to focus the laser beam by bending the light into a more concentrated beam.
This allows the laser to achieve greater accuracy and power when cutting through materials. Cylindrical lenses are used to spread the laser beam into a more evenly distributed beam, which helps to prevent damage to the material being cut. Aspheric lenses are used to create a more uniform beam, which is essential for engraving.
The quality of the lens influences the cutting quality!
The quality of the lenses used in laser cutting machines has a direct impact on the accuracy and precision of the machine. Poor quality lenses can lead to inaccurate results or even damage the material being cut. To ensure the highest quality results, it is important to use lenses that are designed to withstand the high temperatures and powerful laser beams associated with laser cutting.
Danger through decomposition
Thorium fluoride is a chemical compound that can withstand very high heat. For this reason, it is extremely important to protect lenses from contamination. If particles have settled on the lenses, the energy cannot be fully released again. Depending on how dirty the lens is, it disintegrates completely.
When the lens is destroyed, decomposition products such as zinc oxide, selenium oxide and thorium on its surface are released. Thorium and selenium compounds are very toxic and cause serious health problems when inhaled or in contact with skin.
For this reason, lenses should be checked and maintained regularly.
Did you find all the info you need?
Just contact us if you should have further questions!