Corrosion
Corrosion is a natural reaction of metals with oxygen. Corrosion has different forms and can occur in various places. Only knowledge of the many types of corrosion can help to prevent it.
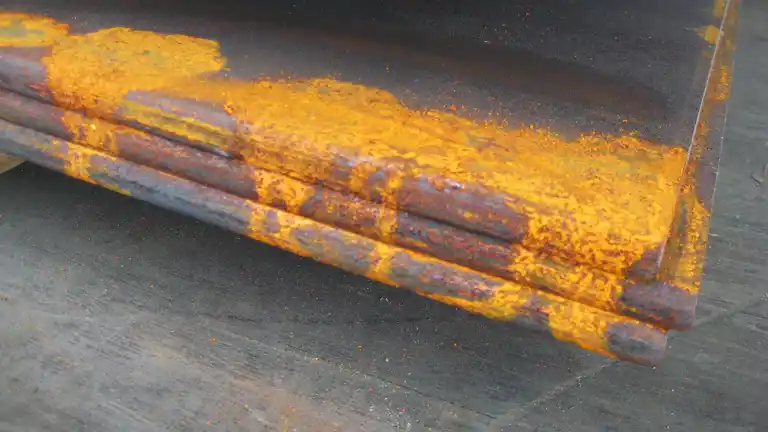
Pitting corrosion
Many types of rustproof steel are very sensitive to chlorine. Chlorine molecules are much smaller than oxygen molecules and can affect the surface of rustproof steel. This causes a flat pitting corrosion, which develops into a deeper pitting corrosion over time.
Pitting corrosion can be prevented by adding molybdenum. A good example is rustproof steel 304, which does not contain molybdenum as an alloying element. 316 stainless steel, which contains (2%) molybdenum as an alloying element, is therefore more resistant to pitting corrosion.
The same type of phenomenon can also occur with other surface contaminants, such as contamination with steel dust. Due to this contamination, the chromium oxide skin cannot completely form and an opening is created through which the iron particle can oxidize and slowly "work its way in". Pitting corrosion is also the result. This can be prevented to a certain extent by pickling and passivating the rustproof steel after processing. During pickling, you can remove the iron particles chemically, after which the passivation ensures that the chromium oxide skin forms again in a controlled manner.
Intercrystalline Corrosion
In addition to pitting corrosion, intergranular corrosion is a common form of oxidation of rustproof steel.
This is due to the fact that only 0.02% carbon can be bound in austenite. The remaining carbon then bonds with the existing chromium and forms chromium carbides. Since chromium and carbon bind together very easily, there is too little chromium to form stainless steel in the areas where chromium carbides are formed.
As mentioned above, rustproof steel should contain at least 10.5% chromium. If the chromium content is too low, the corrosion resistance is insufficient. Since these chromium carbides form along the grain boundaries, (local) oxidation can take place there. Intercrystalline corrosion can be prevented by adding titanium or by reducing the carbon content.
The addition of titanium causes that the titanium, which binds itself to carbon even more easily than chromium, binds the remaining carbon, so that no more chromium carbides can be formed. During welding, however, the titanium can burn, resulting in a very sharp edge with chromium carbides at the edge of the weld. These edges are also called "knife line attacks". A better solution could be to reduce the percentage of carbon to such an amount that it can be completely absorbed in the austenite. In such cases it is better to choose 316L stainless steel instead of 316Ti stainless steel. 304 stainless steel is also available in a reduced carbon version (304L stainless steel).
Stress Corrosion
Stress corrosion is one of the most dangerous forms of corrosion and occurs as a result of a combination of (always) 3 factors:
- A tensile stress on the material
- An aggressive environment for the material in question (e.g. effect of chlorine)
- A material that is sensitive to stress corrosion
Without the corrosion, the material can withstand much higher tensile stress. Without this stress the material would not corrode. The main disadvantage of this form of corrosion is that the material fails without warning and unexpectedly. This often happens at lower loads that the material could normally handle without any problems. Stress corrosion can occur in all types of materials and in different environments.
Crevice Corrosion
Crevice corrosion can occur when two parts are assembled together. The small space between the parts can promote the accumulation of a liquid, e.g. water, by capillary action. An example of such a situation can be found in pipes connected by flanges.
The alloying element molybdenum can counteract this form of corrosion to a certain degree. The best way to prevent this form of corrosion is to seal the gap with a welding seam or other sealing agent.
Nowadays, there are also duplex variants with a higher nitrogen and nickel content. These super duplex variants can be resistant to crevice corrosion.
Crevice corrosion can also occur in very small cracks in stainless steel. These can occur, for example, when the rustproof steel cools down after welding as the material contracts again. The most dangerous aspect of crevice corrosion is that it is practically invisible to the naked eye, so visual inspection is usually insufficient.
See also
Brinell hardness test
Performing the hardness test by means of a ball pressure test according to the Swedish engineer Johann August Brinell.
Read moreCoil
Plate metal that is rolled-up to coils is easier to transport and requires less space in the warehouse
Read moreHistory of Metal Processing
Thousands of years ago, man began to work with gold - today we work with high-strength steels.
Read more