MIG Welding
MAG welding uses active gases and primarily joins steel, whereas MIG welding uses inert gases to weld non-ferrous metals.
MIG welding (metal welding with inert gases) is a process that is referred to as arc welding.
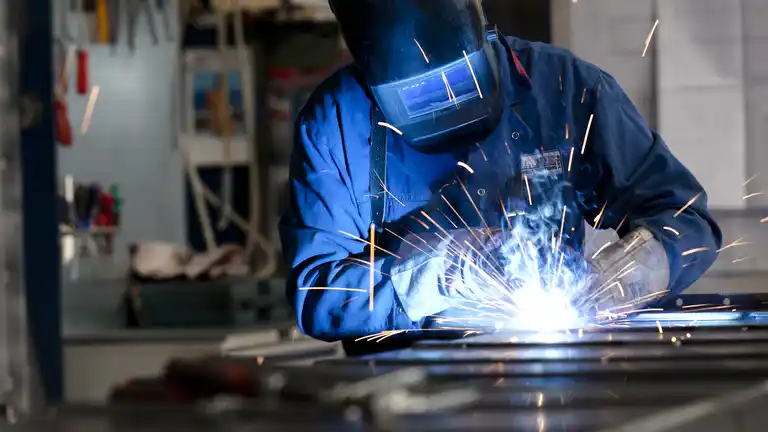
The noble gas that is used here is argon, in rare cases also helium (which is more expensive) or mixtures of these. As the gases used do not react with the base and filler materials, MIG welding is mainly used for joining copper, aluminium or aluminium alloys and other non-ferrous metals.
The inert gases allow welding at much higher temperatures. This eliminates the possibility of oxidation of the weld seam, which is very beneficial.
The welding wire is continuously and automatically unwound from a spool by means of a motor at a variably adjustable speed. By using a contact sleeve, the wire is fed directly and immediately to the welding point. The welding wire melts immediately. During the MIG welding process shielding gas is supplied through a nozzle. This prevents oxygen from penetrating into the weld pool and protects against oxidation. This would lead to a weakening of the weld seam and consequently to inferior quality. The finished weld seam is also called welding bead.
This type of welding is used in the production of containers and pipelines, in mechanical engineering, precision engineering or nuclear technology.
Advantages
No slag is produced during MIG welding. The shielding gas protects the weld seam from the influence of oxygen and thus prevents the risk of oxidation. Due to the high working speed, there is little heat effect on the materials to be welded. Only slight deformations occur.
Drawbacks
If MIG welding were to be used outdoors, it would inevitably lead to the shielding gases being blown away. Therefore this metal shielding gas welding can only be carried out in closed rooms. It is not easy to master and requires a lot of experience.
Contact us!
Call or write us an email if you have questions about welding or need a quote!