MAG Welding
MAG welding, just like TIG welding, belongs to the arc welding processes. MAG welding (with active gases) uses a gas mixture of argon, carbon dioxide and oxygen.
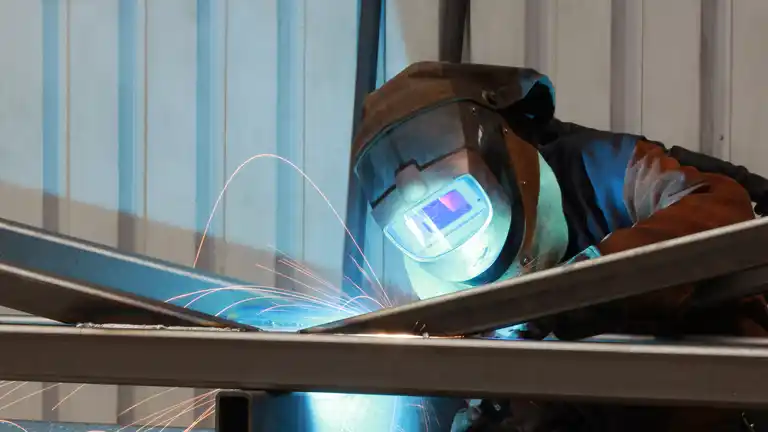
Protective gases can be both inert or active. Inert gases shield the weld pool from the negative influence of oxygen. However, active shielding gases themselves contain a certain amount of oxygen, which acts as an oxygenating additive during welding. Oxygen stabilises the arc and causes the flowing transfer of material to the welding area. The proportions of the individual gases can be adapted to the requirements of the material that is to be welded. This reduces side effects such as burn-in and spattering. MAG welding is mainly used for unalloyed steel grades.
Inert gases offer the advantage that welding can be carried out at higher temperatures without oxidising the material. MAG welding cannot be used outside of closed rooms. The shielding gas could be blown away by wind and weather so that the welding process would take place without protection against oxidation. This weld would then be of inferior quality, susceptible to rust and far less stable.
Very often this type of welding is used in the manufacture of motor vehicles, tanks and pipelines or in mechanical engineering. Even in shipbuilding, MAG welding has become an essential process. Due to the fast welding speed, only slight deformations are expected, even in difficult or awkward positions. Therefore, this arc welding process is mainly used in the thin sheet metal range from 0.6 mm for repairs or maintenance. There is a high strength of the weld seam. Therefore, reworking is almost not necessary.
A motor automatically unwinds a welding wire from a spool and automatically feeds it to the welding point. This wire is fed through the contact sleeve directly to the welding area. In contrast to tungsten inert gas welding (TIG), the welding wire melts away. At the same time shielding gas is fed through a nozzle, which protects the weld pool from the influence of oxygen and thus ensures an oxidation-free connection of the metal parts. The finished weld seam is also known as a welding bead.
Advantages
The weld seam is protected against oxidation. No slag is formed. The working speed is very high. This results in less heat influence of the surrounding material. This method can be used in all welding positions. Because of these special advantages, it is the most used welding method today.
Disadvantages
Wind susceptibility - gas-shielded metal arc welding cannot take place outdoors. MAG welding requires a lot of experience and is not easy to control. The weld seam must also be cleaned of rust beforehand. In addition to appropriate protective clothing, special attention must be paid to proper eye protection, due to the fact that the welding flame develops a remarkably bright arc.
Contact us!
Call or write us an email if you have questions about welding or need a quote!