Milled Parts
As an experienced provider of milling services, Rime specialises in milling various types of metal such as steel, stainless steel, wear-resistant sheet metal and aluminium. We have an extensive machine park, with two modern milling machines.
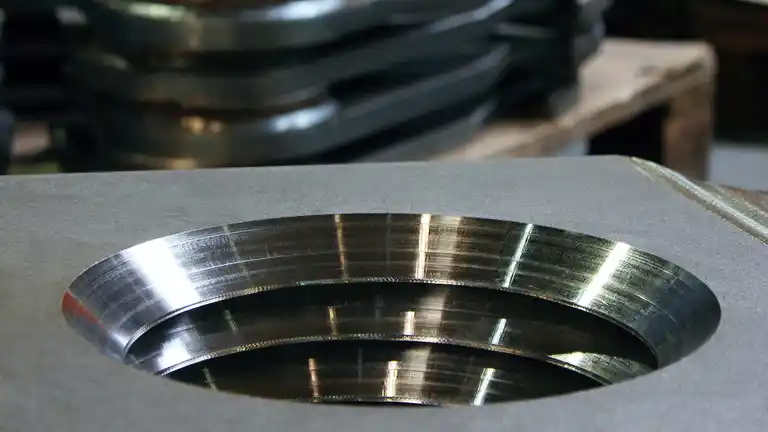
We offer the following advantages:
- Large milling tasks 4,200/3,630 x 750 x 500 mm (XYZ)
- 5-axis milling up to 1,100 mm
- Efficient clamping with magnetic beds & zero clamping system
- Milling of welded constructions, complex workpieces and long workpieces
- Large sheet metal workpieces and serial production
- CNC-controlled milling, drilling, face milling and thread cutting
- Fast and reliable delivery
Get in touch with us!
As a contract manufacturer we can produce parts to your specifications!
Milling holes
Holes are often made by us by Laser cutting. However, there is a rule of thumb that states that the diameter must be at least equal to the material thickness. In exceptional cases and very good material quality, the actual radius can be slightly smaller than this radius. The large amount of heat produced by the laser beam causes scaling on the underside of the metal sheet if the radii are too small. Time-consuming rework is then necessary to remove the scale. The material driven out to make the hole can also deposit on the edge of the hole.
If the material is highly reflective, the laser cannot cut through the material and is reflected back instead. In this case holes have to be drilled. This can be done up to a diameter of 32 mm. Larger holes are then made by milling.
Milling chamfers
One method of making Chamfers is milling. Virtually any chamfer angle can be made by rotating the milling head without causing knurling to occur at the workpiece edges. This is especially interesting for workpieces that are not welded.
With our machining centre we can mill chamfers with all angles. We have suitable tools for several standard angles, which reduces the machining time considerably. Other chamfers are also no problem. They are milled gradually.
In the case of stepped chamfers, choosing the correct milling head is decisive for quality. It is necessary to consider for what the chamfer is needed and what degree of position is required. If it is only the angle that is important and the surface is secondary, the steps can be made somewhat wider.
This saves machining time. In the case of chamfers that need both a precise angle and an absolutely smooth surface, the stepping can be made so fine that no machining pattern remains.
Milling of fits / clearances
Fits can be made using different production methods, depending on their requirements. When choosing the production method the tolerable clearance between the hole and shaft is decisive. If fits are required in the agricultural sector, a larger clearance or allowance is possible as for fits in vehicle and engine construction. Very precise fits can be made by drilling, which have a roughness depth (peak to valley height) of 16 to 250 micrometres.
Milling is a far more precise production process and can achieve roughness depths of up to 1.6 micrometres. With our milling we can make very high-quality fits, which satisfy the highest standards.
Thread milling
With our machining centre we can make high-precision Threads in components. One advantage is that different size threads can be made with the same tool. As the milling takes place with little pressure, threads can also be made in thinner workpieces.
We can basically mill threads of all sizes. Our technicians will be pleased to advise you on which maximum thread sizes are possible in relation to the workpiece size and still have a high mechanical load capacity.
Weld preparation by milling
In classic weld preparation we mill a chamfer at the material edges. The milling produces very clean surfaces, which can then be welded together extremely well.
The chamfered angle helps the welder to join the assemblies. Variable chamfer angles and surface sizes can be produced depending on the customer’s wishes.
Milling chamfers is a relatively expensive method of weld preparation. In order to keep the unit price low, we use a preparation machine especially purchased for this task.