Steel Grades
Today, several hundred different steel grades exist, which differ according to the many different compositions of their alloy elements. Depending on the planned place of use, steel grades with different properties must be chosen.
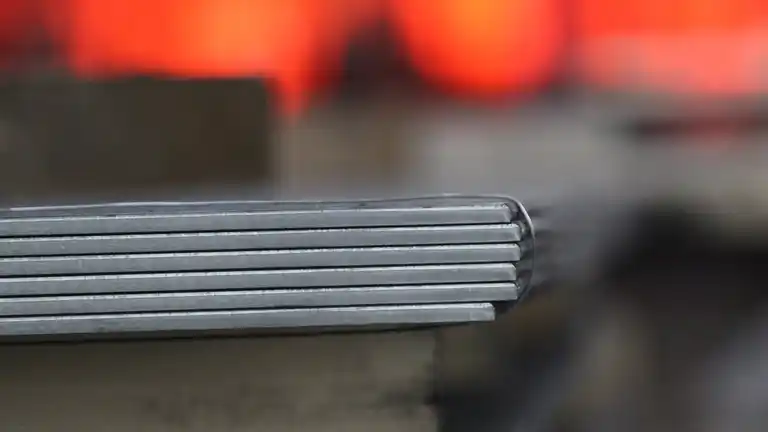
Apart from steels that are not susceptible to rust, among other things, steels that are not susceptible to acid or are salt water resistant are also required. In places with extreme heat, steel grades have been developed that do lose less of their strength at room temperature and are tested at high temperatures.
Unalloyed steel
Unalloyed steels are defined as all iron-carbon alloys which have a carbon content of 0.05 to a maximum of 2% and contain, besides iron, only the natural iron companions such as sulphur, manganese and phosphorus. During the melting process, the proportion of the individual companions can be changed, for example by adding lime to the melt. This lime forms a slag in the blast furnace, in which impurities and undesirable accompanying elements can be removed from the molten steel.
Depending on the composition and concentration of the steel companions, properties such as hardness and tensile strength can be increased or decreased. Unalloyed steels are frequently used for tools and in mechanical engineering.
Alloyed steel grades
Among the alloyed steel grades, a differentiation is made between low-alloy and high-alloy steels.
Low alloyed steels
Low alloy steel grades are marked with the content analysis. The contained elements and their proportions of the steel grade are indicated. The concentration must be written down in whole numbers. All values that are below one percent must be multiplied by a certain factor.
The factor 100 is applied to carbon, chromium and nickel have a factor of 4 and rarer elements such as molybdenum and vanadium must be multiplied by 10.
High-alloyed steels
In principle, the steel grades for high-alloyed steels have the same structure. As the concentration of the individual elements is over 5% there is no need to multiply them with individual factors. The only exception is carbon, which continues to be multiplied by the factor 100. The prefix X is used in order to distinguish high-alloyed steels immediately from other steel grades.
Example
We have a steel with 0.15% carbon, 1.0 % chromium and 0.4 % molybdenum. Theoretically, the steel grade should be 0.15 CrMo 1-0.4 – but this is not allowed. Multiplied by the factors the correct designation is 15 CrMo 4-4
Example
The correct steel grade is X10 CrNi 18-8 for a steel with 0.10 % carbon, 18% chromium and 8% nickel.
See also
Brinell hardness test
Performing the hardness test by means of a ball pressure test according to the Swedish engineer Johann August Brinell.
Read moreCoil
Plate metal that is rolled-up to coils is easier to transport and requires less space in the warehouse
Read moreCorrosion
Corrosion is a natural process and damages most metals. What types of corrosion are there?
Read more