Milling
We have three machining centres. We are well equipped for milling plates. These machines can produce chamfers, fits, recesses, high precision threads and bearing seats. For milling, we have a range of tools in an interchangeable magazine that can be automatically changed as required. This allows fast machining without long changeover times.
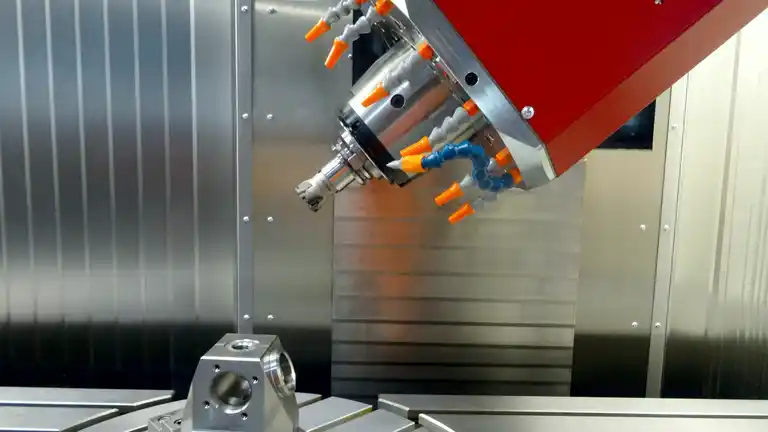
Milling and machining at Rime
- Milling of holes up to a diameter of 32 mm
- Production of standard chamfers with the angle inclinations of 30°, 45° or 60°
- Stepwise milling of chamfers with individual angle inclinations
- Milling with a roughness up to 1.6 microns
- Production of threads
You have a question about our production capabilities?
We are happy to help you! Call us or simply write an E-Mail.
Milling metal sheets
Various tools are available for milling in a changer magazine, which can be exchanged automatically if necessary. This enables speedy machining without lengthy retooling times. With these tools we can make bearing seats, chamfers, fits, cutouts and openings and high-precision threads. The milling is carried out by tools that are fitted with indexable inserts. These inserts are made of extremely resistant steels, which have far higher hardnesses than the workpieces to be machined. The indexable inserts remove material from the surface of the sheet metal part by fast rotation. The required shaped element is therefore produced chip for chip. For this reason, this process is also called chip removal.
You would like to receive an offer? - No problem!
Send us a short E-Mail with your wishes.
Our sister company Tosec offers even larger 3D milled parts up to 7,000 x 1,200 x 1,300 mm. 5-axis machining is possible up to a size of 1,250 mm.
EasyMillDrill - Automated Milling and Machining
From now on we have an automated machining center in our production.
Starting situation
Until now, workpieces were placed in the machine manually or with the help of a crane and then removed again after processing. This activity is physically exhausting and monotonous, especially in series production.
Our sister company Teqram specializes in the automation of machines and production facilities and has created EasyMillDrill, a system that independently takes over the loading and unloading process of machining centers.
After machining, the workpiece can be rotated with the aid of an EasyFlipper so that the reverse side can also be machined if necessary. Once the workpiece is finished, the robot places it on a provided pallet.
This robot system is able to adjust automatically to changes in its work area. For example, if a pallet is moved, the robot recognizes the new position and adjusts to the new situation independently.
Your advantage
The robot can easily handle workpieces weighing up to 100 kg. At the same time, it takes much less time compared to a human operator, which means that the machining center is used more efficiently. Series production of milled parts takes place at a significantly higher speed. In addition, the potential for errors is minimized.
Will the robot take away someone's work?
No. The robotic system will not replace a human worker. The robot will merely take over a tedious and boring task. In addition, the risk of injury will be significantly reduced because there will no longer be a person to handle heavy workpieces. We have much more interesting tasks that our employees will take over in the meantime.
Did you find all the info you need?
Just contact us if you should have further questions!