Laserschneiden: Ihr kompetenter Lohnfertiger für Laserzuschnitte
Wir sind Ihr Partner für präzises Laserschneiden – von Kleinteile bis XXL-Teile, Überlängen und dünne sowie dicke Bleche von bis zu 40 mm. Mit modernster Technologie bearbeiten wir Stahl, Edelstahl und Aluminium effizient und wirtschaftlich. Ob Einzelanfertigung oder Serienproduktion, einfache oder komplexe Geometrien – unsere leistungsstarken Anlagen liefern filigrane Konturen und exakte Schrägschnitte. Verlassen Sie sich auf über 30 Jahre Erfahrung in der Blechbearbeitung, zertifizierte Prozesse und eine europaweite Lieferung.
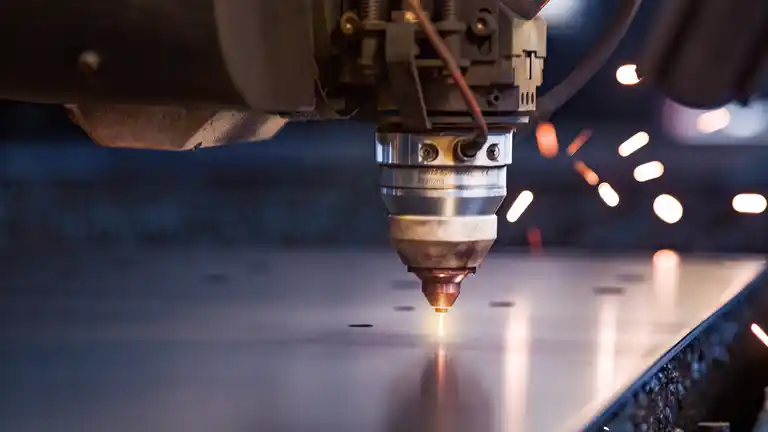
XXL-Laserschneiden für großformatige Bauteile
Hochwertige Zuschnitte aus überdimensioniertem Blech – saubere Schnittkanten ohne Verzug
- Leistungsstarker CO²-Laser (6.000 W)
- Bis zu 16.000 x 4.000 mm für großformatige Bauteile
- Präzise Fasenbearbeitung bis 45°
- Schnittgeschwindigkeit: bis 4 m/min
- Saubere Schrägschnitte
- Exakte Kantenbearbeitung
Schweißnahtvorbereitung per Laserschnitt
Die Schweißnahtvorbereitung ist eine zeitaufwändige Tätigkeit, die für Baugruppenfertigung fast nicht umgänglich ist. Mit unserem XXL-Laser ist es möglich, schon während des Schneidprozesses die Fase anzulegen. Auch das Schneiden von Fasen bei Ronden wird souverän gemeistert.
Jetzt Laserzuschnitt beauftragen
Egal, für welche Form der Kontaktanfrage Sie sich entscheiden - wir melden uns innerhalb von 24 Stunden bei Ihnen!
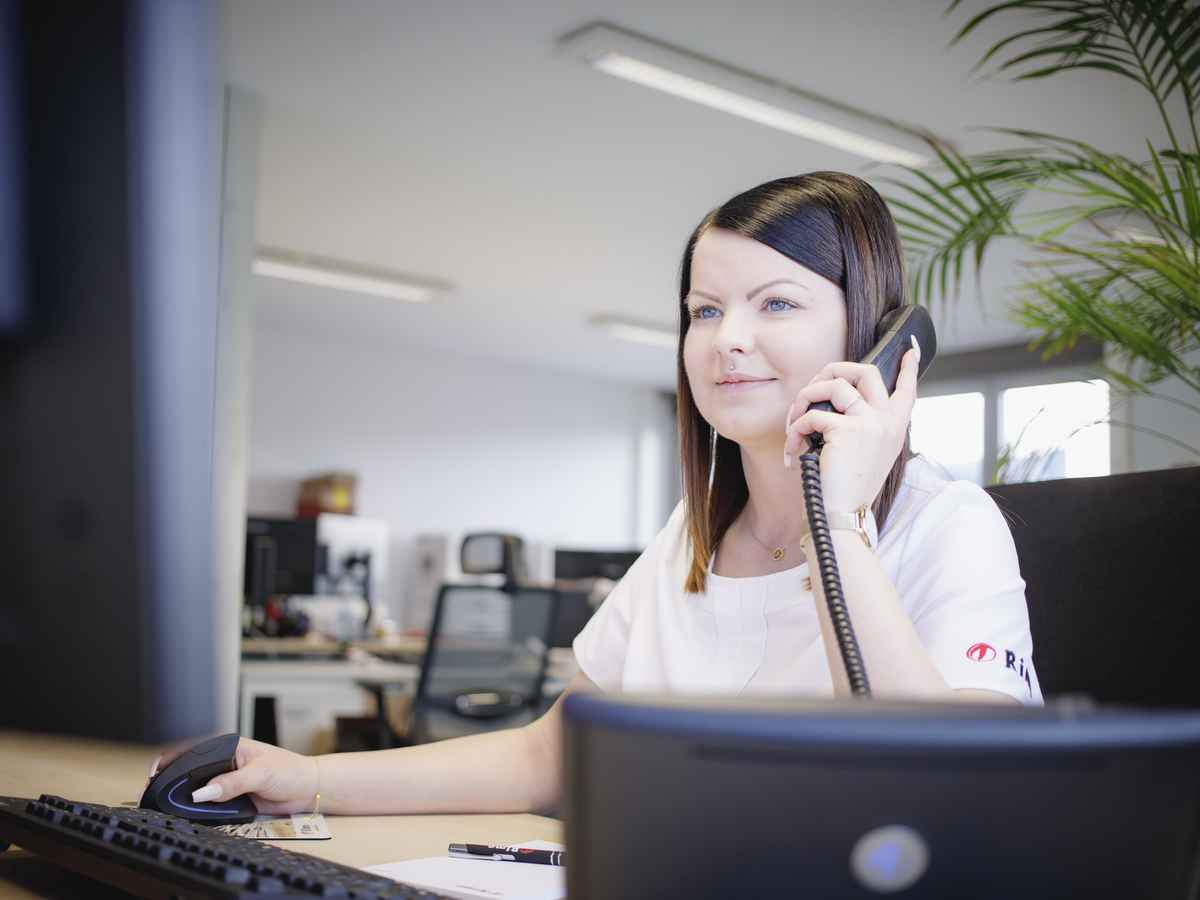
Kontaktieren Sie uns jetzt!
Bei Rime stehen individuelle Beratung und passgenaue Lösungen im Mittelpunkt. Unsere Experten begleiten Sie von der Planung bis zur Fertigung – zuverlässig, effizient und mit höchster Qualität.
Produktbeispiele unserer Fertigung
Die Rime GmbH steht für höchste Verarbeitungsqualität - das sehen Sie auch an nachfolgenden Produktmustern. Passende Beispiele für das Laserschneiden sind benötigte Einzelteile für den Maschinen- und Stahlbau, Verkleidungsteile für den Sonderfahrzeug- oder Schaltschrankbau oder auch Komponente für komplexe Baugruppen aus allen Branchen.
Welches Material wollen Sie zuschneiden lassen?
Wir bieten Laserzuschnitte für verschiedenste Anwendungen, darunter XXL-Teile, Überlängen, Kleinteile oder auch dünne Bleche, für eine Vielzahl von Materialien.
Hier finden Sie eine Übersicht der Werkstoffe, die wir verarbeiten und lagermäßig führen, inklusive der maximal bearbeitbaren Spezifikationen des jeweiligen Materials:
Stahl
Maximalgröße und -dicke:
- 16.000 x 4.000 mm bis 20 mm
- 6.000 x 2.000 mm bis 35 mm
- kleinere Formate bis 40 mm
Materialtypen:
- S235JR 1.0038
- S355J2 1.0577
- S355MC 1.0976
- S700MC 1.8974
- DC01 1.0330
- DD11 1.0332
- Hardox 450
Edelstahl
Maximalgröße und -dicke:
- 16.000 x 4.000 mm bis 12 mm
- 6.000 x 2.000 mm bis 35 mm
- kleinere Formate bis 40 mm
Materialtypen:
- 1.4301 X5CrNi18-10 (V2A)
- 1.4404 X2CrNiMo17-12-2 (V4A)
- 1.4541 X6CrNiTi18-10 (V2A)
- 1.4571 X6CrNiMoTi17-12-2 (V4A)
Aluminium
Maximalgröße und -dicke:
- 6.000 x 2.000 mm bis 40 mm
Materialtypen:
- EN AW-5754 3.3535 AlMg3
- EN AW-5005A 3.3315 AlMg1
- EN AW-6082 3.3547 AlMg4,5Mn
- EN AW-3005 3.0525 AlMg1Mg0,5 H44
- EN AW-6060 3.3206 AlMgSi
Je nach Material setzen wir unterschiedliche Schneidgase ein, um optimale Ergebnisse beim Laserschneiden zu erzielen. Sauerstoff wird für Stahlblech ab 15 mm Dicke verwendet, während Stickstoff bei Edelstahl, Aluminium, Buntmetallen und optional auch bei dünnen Stahlblechen (unter 15 mm Dicke) zum Einsatz kommt.
Zusätzlich können, abhängig vom Material, weitere Bearbeitungsschritte erforderlich sein, um ein perfektes Ergebnis zu erzielen. Schneidgrate, die während der Laserbearbeitung entstehen, lassen sich durch Entgraten bzw. Kanten brechen beheben – sollten weitere Bearbeitungsschritte nach dem Laserschneiden gewünscht sein, lassen Sie es uns gerne in Ihrer Anfrage wissen.
Alle Laserschneiden-Spezifikationen auf einen Blick
Finden Sie hier die wichtigsten Vorgaben und Konstruktionsdetails für das Laserschneiden →
Modernster Maschinenpark und Lasertechnologie
Mit modernster CNC-Technik und innovativen Laserschneidverfahren bieten wir Ihnen maßgeschneiderte Lösungen für den individuellen Metallzuschnitt – präzise, effizient und in herausragender Qualität. Ob feine Konturen oder großformatige Zuschnitte, unser hochmoderner Maschinenpark deckt nahezu alle Anforderungen ab.
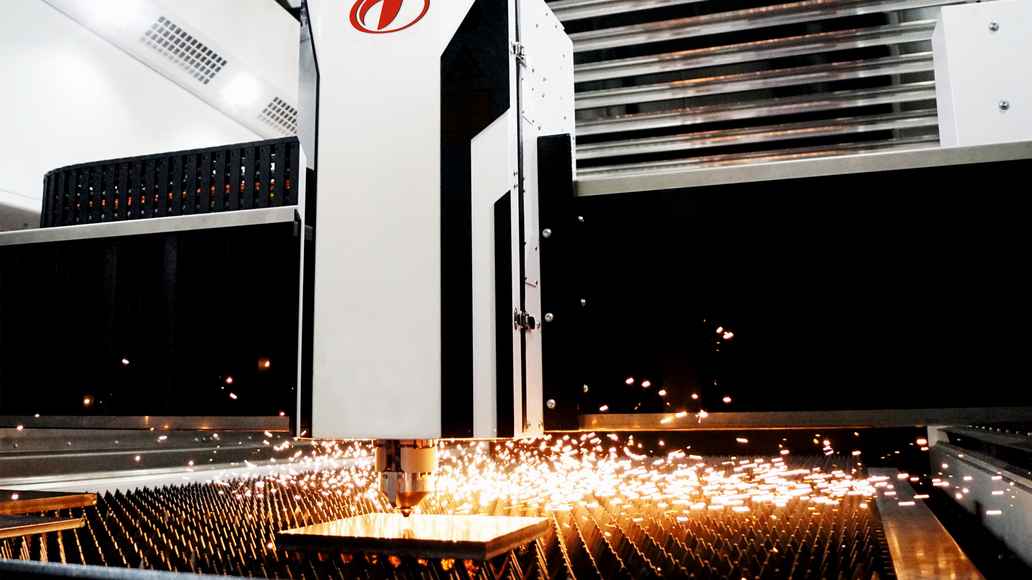
High Power-Fiberlaser statt Plasmaschneiden
In den letzten Jahren hat sich der Markt für thermisches Schneiden rasant weiterentwickelt.
Während Laserschneidemaschinen früher bei einer Materialdicke von rund 30 mm an ihre Grenzen gerieten, waren Plasmaschneidanlagen lange Zeit die bevorzugte Lösung für stärkere Bleche. Mit dem Einzug leistungsstarker Fiberlaser hat sich dieses Bild grundlegend verändert: Moderne Anlagen mit bis zu 30.000 Watt Schneidleistung ermöglichen heute die Bearbeitung von Blechstärken bis zu 100 mm – präzise, schnell und zuverlässig.
Ein wesentlicher Vorteil der Fiberlasertechnologie ist die exakte Schnittführung bei gleichzeitig hoher Schnittgeschwindigkeit. Im Vergleich zum Plasmaschneiden fällt die Wärmeeinbringung deutlich geringer aus, was zu einer verbesserten Schnittqualität führt und das Material schont. Fiberlaser gibt es in zahlreichen Ausstattungsvarianten und Qualitätsstufen – von kosteneffizienten Basismodellen bis hin zu High-End-Lösungen für höchste Anforderungen. Ihre Vielseitigkeit macht sie zum echten Allrounder und dünne Bleche lassen sich ebenso präzise schneiden wie dicke Materialien.
Darum Rime
Schnelle und effiziente Fertigung
Durch den Einsatz modernster digitaler Technologien und einem weitreichenden Produktionsnetzwerk garantieren wir kurze Bearbeitungszeiten – egal, ob es sich um Einzelanfertigungen oder Großserien handelt. Prototypen realisieren wir innerhalb von 7 bis 12 Werktagen, während Serienaufträge durch ein Produktionsplanungssystem getaktet werden, um eine Just-in-time-Produktion zu gewährleisten.
Höchste Präzision und vielseitige Bearbeitungsmöglichkeiten
Unsere fortschrittlichen Verfahren sorgen für millimetergenaue Zuschnitte und Bearbeitungen verschiedenster Materialien wie Stahl, Edelstahl und Aluminium. Mehrere Aufträge werden parallel abgewickelt, wodurch sich Produktionszeiten verkürzen und eine konstant hohe Qualität sichergestellt wird.
Flexibilität und verlässliche Planung
Wir bieten maßgeschneiderte Lösungen mit anpassungsfähigen Produktionskapazitäten, sodass auch spezielle Anforderungen optimal umgesetzt werden. Langfristige Vertragsmodelle ermöglichen stabile Preise und eine zuverlässige Materialbeschaffung für Ihr Unternehmen.
Pünktliche Lieferung und höchste Zuverlässigkeit
Dank optimierter Abläufe und einer eigenen Logistikstruktur garantieren wir eine fristgerechte Zustellung. So profitieren Sie von maximaler Planbarkeit und einer zuverlässigen Lieferung, die Ihren Produktionsprozess nicht ausbremst.
Infobox
Die Rime GmbH besitzt geeignete Maßnahmen zur sachgemäßen Umstempelung von Erzeugnissen mit Bescheinigungen über Werkstoffprüfungen vom Hersteller. Die Regelungen sind entsprechend dem Regelwerk "Druckbehälterrichtlinie 97/23/EG und AD 2000-Merkblatt W 0". Dadurch sind wir in der Lage, Ihre Schneidarbeiten mit 100%iger Rückverfolgbarkeit auszuliefern. Dies ist notwendig, um konform nach DIN EN 1090-2 /-3 EXC2, DIN EN ISO 3834-3 und DIN 2303 Q1 BK2 zu fertigen.
Weitere Informationen oder direkt Anfrage stellen?
Kontaktieren Sie uns gerne für eine Beratung oder fragen direkt Sie Ihr individuelles Projekt an.
Was ist Laserschneiden?
Laserschneiden ist ein präzises Trennverfahren zur Bearbeitung von metallischen Werkstoffen. Ein gebündelter Laserstrahl erhitzt das Material so stark, dass es schmilzt oder verdampft, wodurch ein sauberer Schnitt entsteht. Da der Laserstrahl berührungslos arbeitet, gibt es keine mechanische Belastung, Verformung oder Werkzeugverschleiß bei der Anwendung am Material. Das Laserschneide-Verfahren ermöglicht daher feine, exakte Schnitte und ist besonders effizient für komplexe Formen und verschiedene Materialstärken.
Die Vorteile des Laserschneidens
Laserschneiden ist ein besonders präzises und schnelles Verfahren zur Metallbearbeitung. Doch neben der hohen Genauigkeit bietet es viele weitere Vorteile:
- Saubere Schnittkanten – gratfrei bis geringe Gratbildung und meist ohne Nachbearbeitung
- Geringe Schnittbreite – ermöglicht filigrane Details, selbst bei dickeren Blechen
- Hohe Schnittgeschwindigkeiten – verkürzt Produktionszeiten und steigert die Effizienz
- Komplexe Konturen – selbst aufwendige Geometrien lassen sich problemlos umsetzen
- Vielseitige Materialbearbeitung - bei verschiedensten Blechformaten
- Wirtschaftlichkeit – minimaler Materialverlust und hohe Automatisierbarkeit senken Kosten
Nebeneffekte des Laserschneidens
Beim Laserschneiden können je nach Material, Blechdicke und Bauteilgeometrie verschiedene Oberflächeneffekte auftreten. Diese sind prozessbedingt und stellen in der Regel keine Beeinträchtigung des Grundmaterials dar. Mit zusätzlichen Verfahren lassen sich störende Nebeneffekte entsprechend unterbinden.
Laserspritzer
Metallspritzer auf der Oberfläche entstehen durch:
- Einstich des Lasers in das Grundmaterial
- zu filigrane Bauteilgeometrie oder -kontur
- Fertigungseinflüsse (Verschachtelung, Lage auf Lamellen)
Sie können durch Entgraten entfernt werden. Wir empfehlen, bei empfindlichen Bauteilen die Option „Entgraten“ direkt bei der Anfrage anzugeben.
Rauheit der Schnittkontur
Je nach Material und Blechdicke können Rillen auf der Schnittfläche auftreten. Diese Rauheit ist ein prozessbedingtes Merkmal und kann nicht durch Entgraten entfernt werden. Der Laserstrahl verliert bei dickeren Materialien eher seinen Fokus. Dies führt dazu, dass der Strahl nicht mehr optimal gebündelt ist und die Schnittfläche unregelmäßiger wird, was sich in den Rillen zeigt.
Microjoints und Nanojoints
Micro- oder Nanojoints sind kleine Hilfsstege, welche das Kippen der gelaserten Teile verhindern sollen. Die Teile bleiben so mit dem Restergitter verbunden. Durch die schnellen Vorschubwerte der Schneideeinheit kann dadurch eine Kollision verhindert werden. Teilweise können die gelaserten Produkte mit wenig Kraft per Hand gelöst und vom Schneidetisch entfernt werden.
Wärmebeeinflusste Zone
Wärmeeinflusszonen spielen eine große Rolle beim Laserschneiden. Ein Faktor ist die Wahl der Schneidtechnologie: CO²- oder Fiberlaser. Prinzipiell erzeugt der Fiberlaser durch den optischen Faserkern eine kleinere Wärmeeinflusszone. Daher ist es sinnvoll, mit dem Fiberlaser dünneres und mit dem CO²-Laser dickeres Material zu schneiden. Bei beiden Prozessen kann es durch zu großenWärmeeintrag zur Aushärtung und Verformungen des Materials kommen.
Oxidschicht
Die Oxidschicht entsteht beim Laserschneiden an der Schnittkante, wenn das Material beim Schneiden mit Sauerstoff in Berührung kommt. Dies hat verschiedene Auswirkungen auf das Endprodukt und dessen Qualitätsansprüche. Durch den Einsatz von Sauerstoff als Prozessgas kann aufgrund der gebildeten Oxidschicht eine Verfärbung der Schnittfläche in einen blauen oder rostigen Farbton auftreten oder sogar eine Nachbearbeitung nötig sein.
Infobox
Für eine optimale Oberflächenqualität empfehlen wir, spezielle Anforderungen bereits in der Anfrage anzugeben, damit notwendige weitere Bearbeitungsschritte direkt mitberücksichtigt werden können und ein optimales Ergebnis garantiert werden kann.
Weitere Informationen oder direkt Anfrage stellen?
Kontaktieren Sie uns gerne für eine Beratung oder fragen direkt Sie Ihr individuelles Projekt an.
Einsatzbereiche und Branchen
In unserer umfangreichen Firmengeschichte haben wir uns ein großes Know-How in verschiedenen Branchen angeeignet.
Der Laserschneidprozess & Einflussfaktoren
Der Laserschneidprozess beruht auf dem präzisen Zusammenspiel verschiedener Komponenten, die den Materialabtrag steuern und beeinflussen. Sehen Sie in der nachfolgenden Abbildung grafisch erläutert, wie das Laserschneiden in der Praxis funktioniert.
- Laser-Resonator - Hier wird der Laserstrahl erzeugt, der die nötige Energie liefert, um das Material zu schmelzen oder zu verdampfen. Die Laserleistung muss exakt eingestellt werden, um eine optimale Bearbeitung zu gewährleisten.
- Umlenkspiegel - Der Strahl wird durch Spiegel exakt zur Bearbeitungsstelle gelenkt. Bei CO₂-Lasern erfolgt dies über ein Spiegelsystem, während Faserlaser das Licht über ein Lichtleitkabel transportieren.
- Fokussierrohr & Fokussierlinse - Der Laserstrahl wird gebündelt und auf einen winzigen Punkt konzentriert, wodurch eine extrem hohe Energiedichte entsteht. Die Fokuslage und der Fokusdurchmesser beeinflussen dabei die Qualität der Schnittkante.
- Schneidgas - Das Gas tritt durch die Schneiddüse aus und entfernt die Schmelze aus der Schnittfuge. Je nach Material kommen Sauerstoff oder Stickstoff zum Einsatz. Sauerstoff ermöglicht schnellere Schnitte, während Stickstoff eine oxidfreie Kante garantiert.
- Schneiddüse - Die Düse steuert den Gasfluss und beeinflusst somit die Qualität des Schnitts. Der Düsendurchmesser bestimmt die Gasmenge und Strömung, was entscheidend für saubere Schnittkanten ist.
- Schnittspalt - Der Laserstrahl durchdringt das Material exakt an der gewünschten Stelle und erzeugt einen feinen, präzisen Schnittspalt. Die Schneidgeschwindigkeit muss je nach Materialstärke angepasst werden, um Gratbildung zu vermeiden.
- Werkstück - Das Material wird lokal erhitzt und entlang der gewünschten Kontur bearbeitet.
Durch die präzise Steuerung dieser Parameter entstehen saubere, wirtschaftliche und hochpräzise Schnitte, unabhängig von Material oder Anwendung.
Welche Laserschneidverfahren gibt es?
Je nach Werkstoff, Anwendung und der Wirkungsweise der eingesetzten Laser wird das Laserschneiden in verschiedene Verfahren unterteilt.
Laserstrahlschmelzschneiden
Beim Laserstrahlschmelzschneiden wird das Material an der gewünschten Stelle
durch den Laserstrahl geschmolzen. Ein Gasstrahl bläst die Schmelze aus der
Schnittfuge, wodurch saubere und präzise Schnitte entstehen. Dieses Verfahren verhindert Oxidbildung und sorgt für eine hohe Schnittqualität.
2D-Laserschneiden
Das 2D-Laserschneiden ist perfekt für flache Materialien wie Bleche. Es ermöglicht die Bearbeitung fast aller Materialien schnell, präzise und kostengünstig, selbst bei kleinen Mengen. Im Vergleich zu herkömmlichen Verfahren wie Stanzen spart es Zeit und Geld.
Laserstrahlbrennschneiden
Dieses Verfahren wird oft für dickere Materialien verwendet. Neben dem Laserstrahl wird Sauerstoff zugeführt, der das Material zusätzlich erhitzt und das Schneiden erleichtert. Die Schmelze wird dabei direkt aus der Schnittfuge entfernt.
3D-Laserbearbeitung
Die 3D-Laserbearbeitung wird für komplexe Formen und dreidimensionale Bauteile verwendet. Diese Technik ermöglicht z. B. das Schneiden von Rohkarosserien oder Durchbrüchen und kombiniert oft mehrere Bearbeitungsschritte in einem Arbeitsgang.
Laserstrahl-
sublimationsschneiden
Beim Sublimationsschneiden wird das Material durch die große Hitze des Lasers direkt in Dampf umgewandelt, ohne dass Schmelze entsteht. Dieses Verfahren ist besonders geeignet für Materialien wie Kunststoffe, die klare und glatte Schnittkanten erfordern.
Rohrlasern
Das Rohrlasern ermöglicht die Bearbeitung von runden, quadratischen oder ovalen Rohren in nur einem Arbeitsgang. Es können Löcher, Konturen und andere Formen präzise und maßgenau in die Rohre geschnitten werden.
Wie findet die Preisbildung beim Laserschneiden statt?
Die Kosten für CNC-Laserschneiden können stark variieren und hängen von mehreren Faktoren ab.
Im Mittelpunkt steht dabei die Komplexität der Bauteile: Je aufwändiger die Geometrie, desto höher ist der Zeitaufwand für den Schneidprozess.
Auch das verwendete Material beeinflusst den Preis maßgeblich. Entscheidend sind dabei:
- Materialart (z. B. Stahl, Edelstahl oder Aluminium)
- Oberflächengüte
- Blechdicke
- Format und Größe des Zuschnitts
Als erfahrener Lohnfertiger setzen wir auf faire und transparente Preise. Jedes Projekt wird individuell kalkuliert – so erhalten Sie ein Angebot, das exakt auf Ihre Anforderungen zugeschnitten ist und ein optimales Preis-Leistungs-Verhältnis bietet.
Anschließende Bearbeitungsverfahren
Sehen Sie nachstehend Metallbearbeitungsverfahren, die auch für Sie relevant sein könnten:
Abkanten | Fräsen | Schweißen | Weitere Verfahren |
---|---|---|---|
Laserteile können im Anschluss abgekantet werden. Dies können wir bis zu einer Länge von 16 m realisieren. |
Um noch mehr Präzision in Ihre Fertigungsteile zu bekommen, können zerspanende Bearbeitungen an unseren 5- und 3- Achsfräszentren vollzogen werden. |
Einzelteile können auch bei uns im Hause durch zertifizierte Schweißprozesse gefügt werden. Das Gesamtgewicht der Baugruppen kann bis zu 50 t erreichen. |
Hier finden Sie die Übersicht unserer Blechbearbeitungs- Verfahren. |
Weitere Informationen oder direkt Anfrage stellen?
Kontaktieren Sie uns gerne für eine Beratung oder fragen direkt Sie Ihr individuelles Projekt an.